Summary
Manufacturing ERP (Enterprise Resource Planning) systems are crucial tools that integrate various business processes under one digital platform, enhancing efficiency and cutting costs in manufacturing operations. These systems automate and streamline processes like production planning, inventory management, and quality control. By implementing an ERP system, manufacturers can achieve significant improvements in operational efficiency, reduce lead times, and improve customer satisfaction. Selecting the right ERP system involves considering scalability, user-friendliness, and specific industry needs. Successful implementation requires careful planning, team involvement, and continuous improvement.
Key Points
- Enhanced Efficiency: ERP systems automate tasks, enabling real-time inventory tracking and optimized production scheduling.
- Cost Savings: Companies report significant reductions in operational and administrative costs after ERP implementation.
- Improved Decision-Making: Real-time data enhances decision-making and responsiveness to market changes.
- Successful Implementation: Requires defining objectives, assembling the right team, assessing current processes, and investing in training.
- Continuous Improvement: Regular monitoring and feedback ensure the ERP system continues to meet evolving business needs.
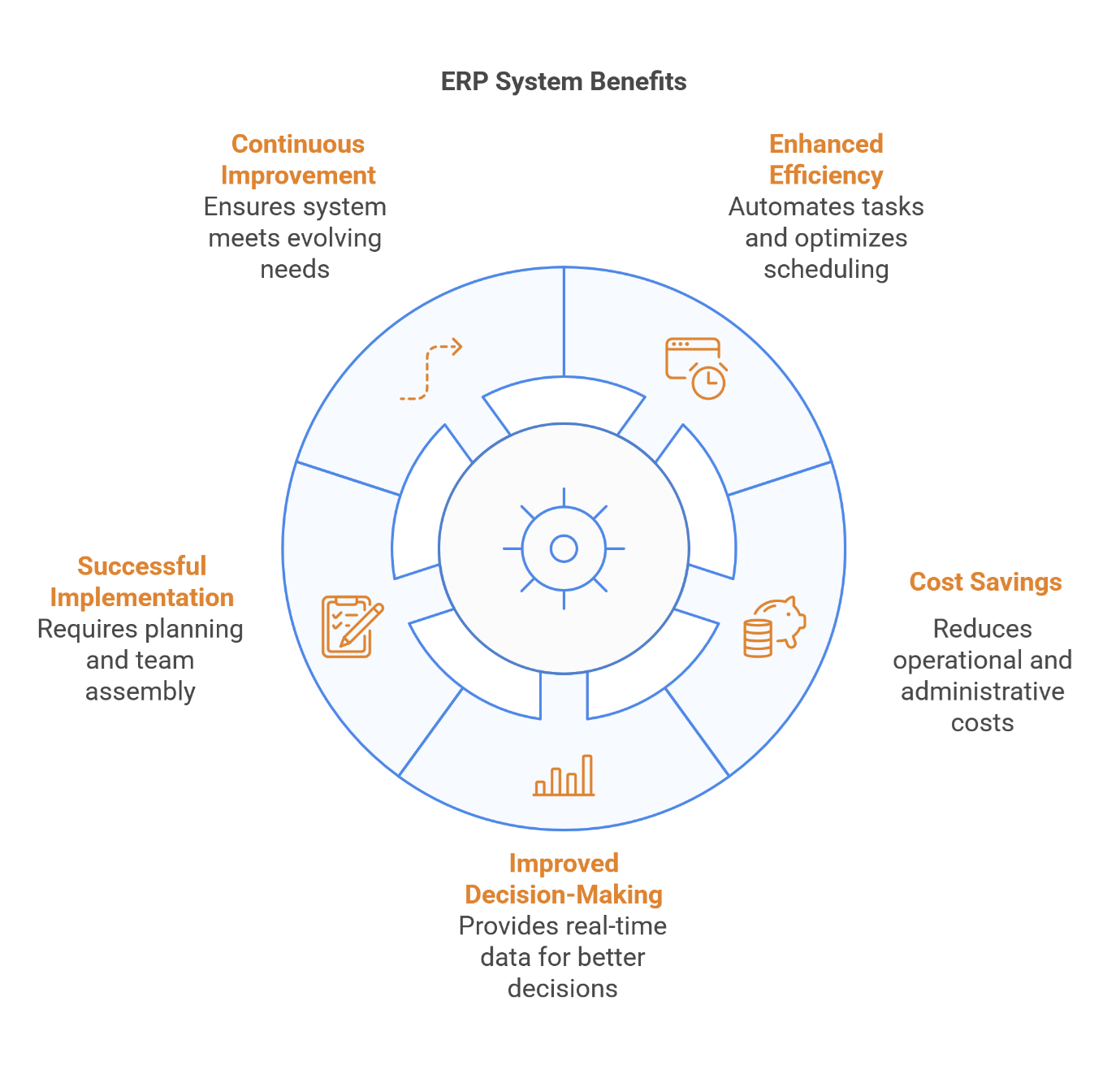
Understanding Manufacturing ERP Systems
Imagine running a manufacturing plant where every process, from inventory tracking to production scheduling, is seamlessly integrated. This is the power of Manufacturing ERP (Enterprise Resource Planning) systems. These systems unite all business processes under one digital roof, allowing manufacturers to streamline their operations and improve efficiency.
With an ERP system, you can automate tasks that once took hours, if not days. For instance, instead of manually tracking inventory levels, an ERP system provides real-time data that keeps you informed about stock availability. This means you can avoid costly delays and ensure that production runs smoothly.
What is Manufacturing ERP?
Manufacturing ERP software serves as a unified platform that connects various functions within a manufacturing business. It integrates key processes such as:
- Production Planning: Helps schedule production runs based on demand forecasts.
- Inventory Management: Tracks raw materials and finished goods to optimize stock levels.
- Quality Control: Monitors production quality to ensure standards are met.
By centralizing these functions, ERP systems reduce the complexity of managing multiple software solutions, leading to better decision-making and improved operational workflows.
The Impact of Digital Transformation
In today’s fast-paced manufacturing environment, digital transformation is not just a trend; it’s a necessity. Implementing an ERP system can significantly enhance your business’s agility and responsiveness to market changes. With real-time data at your fingertips, you can quickly adapt to customer needs and streamline your supply chain.
Consider the case of a small manufacturer that adopted an ERP system. Before implementation, they struggled with inventory shortages and production delays. After integrating ERP, they achieved a 30% reduction in lead times and improved customer satisfaction scores by 25%. This transformation illustrates how powerful an effective ERP system can be for manufacturing businesses.
Choosing the Right ERP System
When selecting an ERP solution, it’s essential to consider your specific needs as a manufacturer. Not all systems are created equal; some are tailored for small businesses while others cater to larger enterprises. Look for features that align with your operational goals, such as:
- Scalability: Can the system grow with your business?
- User-Friendliness: Is it easy for your team to adopt?
- Support and Training: What resources are available for implementation?
For small manufacturers, options like Acumatica ERP offer cost-effective solutions that don’t compromise on functionality. Their cloud-based platform allows for flexibility and easy access to critical data from anywhere.
Manufacturing ERP systems are essential tools for any manufacturer looking to boost efficiency and reduce costs. By integrating various business processes into one unified platform, these systems simplify operations and enhance productivity. As the manufacturing landscape continues to evolve, investing in an effective ERP solution will position your business for success in a competitive market.
By understanding the benefits of Manufacturing ERP systems and choosing the right solution for your needs, you can transform your operations and achieve significant improvements in efficiency and cost management.
Key Benefits of Manufacturing ERP
Manufacturing ERP systems deliver remarkable cost savings and efficiency gains. Companies report 23% lower operational costs and 22% reduced administrative expenses through ERP implementation[2]. These systems transform manufacturing operations by connecting every aspect of production under one digital roof.
Streamlined Production Planning
Production planning shifts from manual guesswork to data-driven precision with ERP systems. Real-time monitoring enables manufacturers to:
- Track machine performance and production status instantly
- Optimize resource allocation based on actual demand
- Reduce production lead times by up to 30%[18]
- Generate efficient schedules that maximize resource utilization[25]
A unified dashboard gives production supervisors complete visibility into resource availability, material requirements, and production schedules[8]. This enhanced control helps prevent bottlenecks and ensures smooth workflow across the factory floor.
Inventory Management Excellence
Smart inventory control through ERP prevents costly stockouts while optimizing carrying costs. An aerospace manufacturer reduced their inventory by $20 million within just 90 days of implementing ERP[18]. The system enables:
- Real-time tracking of stock levels across locations
- Automated reordering based on production needs
- Reduced inventory costs by 25-30%[19]
- Prevention of excess stock and obsolescence
The system’s automated tracking ensures optimal stock levels through:
Feature |
Benefit |
Barcode Scanning |
Accurate inventory counts |
Real-time Updates |
Precise stock visibility |
Automated Alerts |
Timely reordering |
Demand Forecasting |
Optimized stock levels |
Manufacturing companies using ERP report significant improvements in inventory turnover and working capital optimization[6]. The system’s ability to maintain optimal inventory levels while reducing carrying costs makes it an essential tool for modern manufacturers looking to boost efficiency and reduce operational expenses.
Through these integrated capabilities, manufacturing ERP systems create a synchronized environment where production planning and inventory management work together seamlessly, driving both operational excellence and cost reduction. The result is a more agile, efficient, and profitable manufacturing operation.
Real-World Implementation Success
Imagine a manufacturing company struggling with high operational costs and delayed deliveries. That was the reality for Superprem Industries, a mid-sized manufacturer in the furniture sector. They faced challenges like inefficient inventory management and slow production processes, which hindered their growth. But everything changed when they decided to implement Acumatica ERP.
After integrating Acumatica into their operations, Superprem Industries saw remarkable results. They achieved a 20% reduction in operational costs and improved their delivery times by 35%. This transformation didn’t just happen overnight; it was the result of a well-planned ERP implementation strategy that focused on optimizing every aspect of their manufacturing process.
Key Changes Made
- Streamlined Production Management: Acumatica allowed Superprem to automate their production planning. This meant they could schedule jobs more efficiently, ensuring that resources were used effectively and reducing downtime.
- Enhanced Inventory Control: With real-time inventory tracking, Superprem could maintain optimal stock levels. They avoided stockouts and overstock situations, which not only saved money but also improved customer satisfaction by ensuring timely deliveries.
- Data-Driven Decisions: The ERP system provided valuable insights into production metrics and inventory levels. This data helped management make informed decisions quickly, adapting to market demands without hesitation.
- Improved Communication: Acumatica facilitated better communication across departments. Everyone had access to the same real-time information, which helped reduce errors and streamline workflows.
The success story of Superprem Industries is just one example of how effective ERP implementation can lead to significant performance improvements in manufacturing. By transforming their factory floor with data-driven decisions, they not only enhanced efficiency but also positioned themselves for future growth.
“Transform your factory floor with data-driven decisions.”
This quote encapsulates the essence of what Acumatica ERP can do for manufacturers. It’s about leveraging technology to create a more agile, responsive business capable of thriving in a competitive landscape. The journey may require effort and investment, but as Superprem’s case shows, the rewards can be substantial—lower costs, faster deliveries, and happier customers.
Practical Steps to ERP Success
Implementing an ERP system in your manufacturing facility can feel like a daunting task, but it doesn’t have to be. With careful planning and execution, you can ensure a smooth adoption that will transform your operations. Here’s a straightforward guide to help you navigate the process effectively.
- Define Your Objectives
Start by identifying what you want to achieve with your ERP system. Are you looking to reduce costs, improve efficiency, or enhance customer satisfaction? Clearly defined goals will guide your implementation strategy and help you measure success down the line.
- Assemble the Right Team
Create a dedicated project team that includes members from various departments—production, finance, IT, and sales. This diverse group will provide valuable insights into how the ERP can best serve each area of your business. Make sure to include a project manager who has experience with ERP systems.
- Assess Current Processes
Before diving into implementation, take a close look at your existing workflows. Identify pain points and inefficiencies that the ERP system can address. This assessment will help you customize the system to meet your specific needs.
- Choose the Right ERP Solution
Not all ERP systems are created equal. Research and select one that aligns with your manufacturing processes and industry requirements. Look for features like production scheduling, inventory management, and reporting capabilities that are crucial for your operations.
- Plan Your Implementation
Develop a detailed project plan that outlines timelines, responsibilities, and milestones. Break the implementation into manageable phases to avoid overwhelming your team. For example:
- Phase 1: Data migration
- Phase 2: System configuration
- Phase 3: User training
- Phase 4: Go-live and support
- Data Migration and Integration
Migrate data from your old systems carefully. Cleanse the data to ensure accuracy before transferring it to the new ERP system. This step is crucial for maintaining data integrity and ensuring smooth operations post-implementation.
- Training is Key
Invest time in training employees on how to use the new system effectively. Tailor training sessions based on different user roles within the organization. A well-trained staff will be more confident in using the ERP system, leading to higher adoption rates.
- Monitor Progress
Once the ERP system is live, closely monitor its performance against your initial objectives. Use key performance indicators (KPIs) to track improvements in efficiency, cost reduction, and productivity gains.
- Gather Feedback
Encourage users to provide feedback on their experience with the new system. This input can help identify areas for improvement and ensure that the ERP continues to meet your business needs.
- Continuous Improvement
ERP implementation is not a one-time event; it’s an ongoing process. Regularly review how well the system aligns with your evolving business goals and make necessary adjustments or upgrades as needed.
By following these practical steps, you can set your manufacturing facility up for success with an ERP system like Acumatica. The journey may have its challenges, but with careful planning and execution, you’ll reap the benefits of improved operational workflows and reduced costs in no time!
Key Benefits of Manufacturing ERP
Implementing an ERP system can significantly transform manufacturing operations. Companies that adopt ERP solutions often report a remarkable 23% reduction in operational costs and a 22% decrease in administrative expenses. These systems streamline processes, leading to measurable improvements that can redefine how manufacturers operate.
Cost Reduction
One of the most compelling reasons to invest in an ERP system is cost reduction. By integrating various functions, ERP systems eliminate inefficiencies and reduce the need for multiple software solutions. This consolidation can lead to significant savings on software licensing, training, and maintenance costs.
- Automation: Automating routine tasks like inventory tracking and order processing minimizes human error and frees up staff to focus on higher-value tasks.
- Real-Time Data: Access to real-time data allows for better decision-making, reducing the chances of costly mistakes.
Efficiency Gains
Efficiency is at the heart of every successful manufacturing operation. An ERP system enhances productivity by providing tools that facilitate better planning and execution.
- Streamlined Workflows: With all departments connected, information flows seamlessly. This connectivity reduces delays and miscommunication between teams.
- Improved Production Scheduling: ERP systems optimize production schedules based on real-time demand data, ensuring that resources are allocated effectively.
Productivity Improvement
ERP systems empower manufacturers to boost productivity through better resource management and process optimization.
- Resource Allocation: By analyzing data on machine usage and labor availability, manufacturers can allocate resources more effectively, reducing downtime.
- Inventory Management: With automated inventory tracking, companies can maintain optimal stock levels, preventing both overstocking and stockouts. This leads to smoother production processes and improved customer satisfaction.
Streamlined Production Planning
Production planning is critical for meeting customer demands while minimizing waste. ERP systems transform this process from guesswork to precision.
- Data-Driven Decisions: Real-time data enables smarter scheduling and resource allocation, allowing manufacturers to respond quickly to changes in demand.
- Reduced Lead Times: By optimizing production schedules, manufacturers can significantly cut down on lead times, enhancing their ability to meet customer expectations.
Inventory Management Excellence
Effective inventory management is vital for reducing costs and improving operational efficiency. ERP systems provide robust tools for managing inventory effectively.
- Automated Tracking: Smart inventory control prevents stockouts while reducing carrying costs through automated tracking of stock levels.
- Forecasting Capabilities: Accurate forecasting helps manufacturers anticipate inventory needs, ensuring they have the right materials on hand when needed.
By leveraging these benefits, manufacturers can not only reduce costs but also enhance their overall operational workflows. Investing in an ERP system like Acumatica is a strategic move that positions businesses for long-term success in a competitive market.
Wrapping Up
ERP systems like Acumatica are revolutionizing manufacturing operations around the globe. These powerful tools help businesses streamline their processes, cut costs, and enhance productivity. If you’re a manufacturing professional looking to improve your operational workflows, now is the time to start your efficiency journey.
Imagine a factory where every department communicates seamlessly, inventory levels are optimized, and production schedules adapt in real-time to changing demands. This is the reality that ERP systems create. By integrating various functions—such as production planning, inventory management, and quality control—an ERP system provides a single source of truth for your entire organization.
To get started, it’s essential to choose the right ERP solution that fits your specific needs. Consider factors like scalability, user-friendliness, and industry-specific features. Then, focus on a solid implementation strategy that includes training your team and continuously monitoring performance.
By embracing an ERP system, you’re not just investing in software; you’re investing in the future of your manufacturing operations. The journey may require effort, but the rewards—improved efficiency, reduced costs, and enhanced customer satisfaction—are well worth it. Take the first step today towards transforming your manufacturing processes with Acumatica ERP!
FAQ Section:
- Q: How much can ERP reduce manufacturing costs?
A: Manufacturing companies typically see 20-30% cost reduction through improved efficiency and reduced waste.
- Q: How long does ERP implementation take?
A: Implementation usually takes 6-12 months, depending on company size and complexity.
- Q: What ROI can manufacturers expect from ERP?
A: Average ROI is 168% with a payback period of 3.7 years.
- Q: Which manufacturing processes can ERP optimize?
A: ERP optimizes production planning, inventory management, supply chain, quality control, and financial operations.
- Q: Is ERP suitable for small manufacturers?
A: Yes, modern ERP systems are scalable and offer solutions for manufacturers of all sizes. Call to Action: Schedule a free consultation to discover how ERP can transform your manufacturing operations.